As inkjet printing progresses, becoming faster and
more reliable, regulatory questions like food-contact (Swiss Ordinance, etc.)
and health and safety in décor applications (RAL for wallpaper, etc.) play an
increasingly important role. This is where UV-curable inks often reach their
limits, as their composition of reactive chemistry is often not compliant with
health and safety requirements.
Water-based inks can solve this challenge, with a
similar application process as UV-curable inks, but without the non-compliant
materials. Water-based inks are comprised of binders, dyes or pigments, water,
and co-solvents that can be food-contact compliant and fulfil most norms. The
added challenge with water-based inks is that after jetting, the prints need to
dry. The faster the print, the less absorbent the substrate, the more complex
the drying needs are.
At IJC 2019 a consortium of four companies; adphos, Imagexpert, Konica Minolta (IIJ) and Marabu demonstrates the possibilities of water-based inks.
Imagexpert: The leader in systems for inkjet development provides the JetXpert Print Station: an all-in-one drop-watching and sample printing system. This modular system can accommodate any printhead, drive electronics, curing/drying station, and other components to create a development platform for any application. Equipped with the Konica Minolta printhead and Marabu ink, the system can be used for developing different ink formulations, waveform optimization, and analysing wetting, missing jets, and more. When combined with the adphos aNIR dryer, the user can easily print sample images to optimize printing speed, substrate selection, drying power, and more.
Konica
Minolta inkjet printheads have been used with water-based inks for over 20
years. Initially in their Nassenger textile printing products, more recently
the range of water-based applications has widened to include décor, packaging,
document printing and many more.
Industrial Inkjet Ltd, the sales and technical support for Konica Minolta inkjet products outside of Asia, has been working with Marabu and Adphos for several years evaluating solutions for these applications utilising IIJ’s compact print engines that are fitted with either KM1024i or KM1800i printheads. The use of NIR and suitable inks means the complete solution is compact even for high speed printing, making it market leading technology.
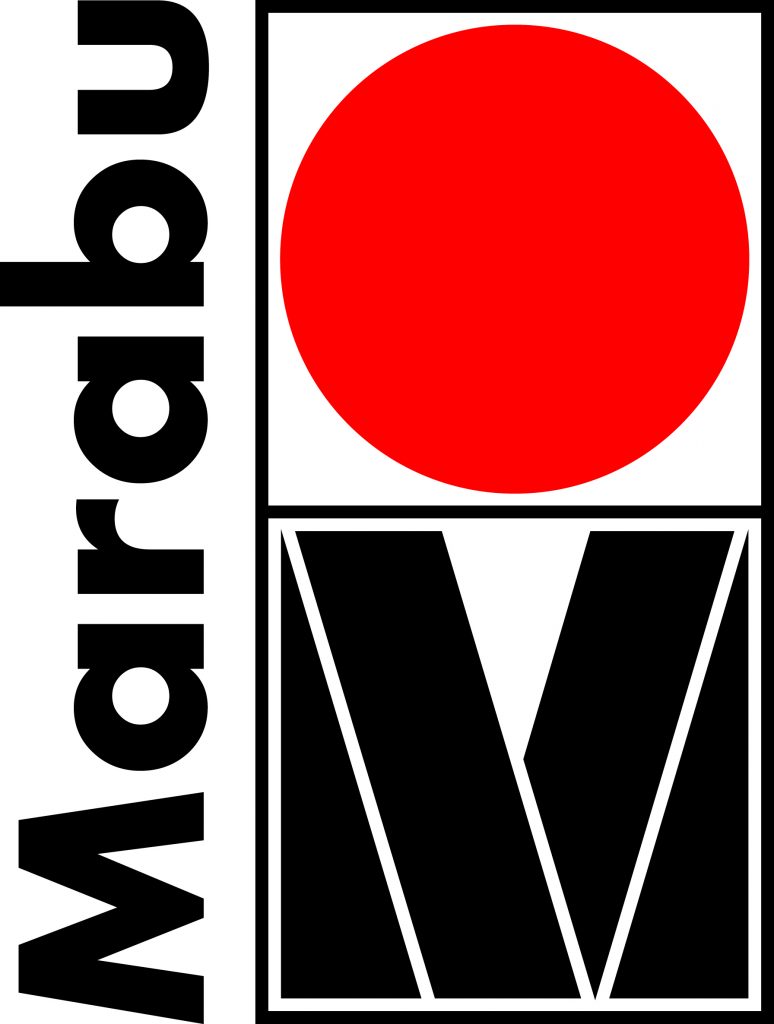
Marabu is a world-leading manufacturer of screen, digital,
and pad printing inks as well as liquid coatings. Thanks to their unique
features, Marabu’s printing inks provide an enormous variety of solutions for
graphic and industrial printing applications. Individually printed wallpapers
hang in living rooms, schools, kindergartens or at the workplace. Therefore,
wallpaper printing should be odourless and free of harmful substances. Important
for wallpaper manufacturers and consumers: Marabu’s water-based digital
printing inks guarantee that the end product is certified according to DIN
15102 and RAL 479 (quality mark for wallpapers).
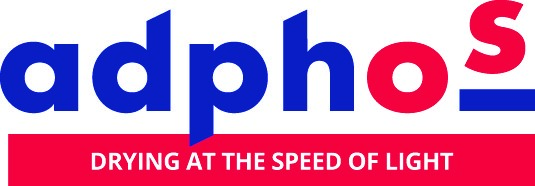
adphos: The Bavarian
technology leader in highly efficient advanced NearInfraRed-drying
“aNIR®” provides the
NIR42-125 for 230V. This versatile entry-level-dryer can be equipped with aNIR®-emitters from
0,5 kW to 2,1 kW. aNIR® systems can vary from 0.2 kW to 20,000 kW and between focussed areas of
Ø 1mm as well as large areas of (3m x 10m) depending on application-optimized
customer-specific process requirements.
aNIR® can be used for heating, forming, drying,
melting and curing processes in a large variety of industrial sectors.
Plastics, steel, graphics, automotive, pharmaceutical, food and semiconductor
industries as well as thermal process engineering, 3D manufacturing and
sintering application benefits from adphos’ advanced NIR process technology.
Within the last 25 years over 2.000 production systems have been successfully
realized